As responsible person in the press shop one depends on the statements of the coworkers regarding the
output potential of tools / sheet metal components, since for own, detailed stocktaking and evaluation usually little or no time is available.
According to Charles Dickens "Even a heavy door needs only a small key" - the potential of a tool / component for more stroke rate can be evaluated in a few moments without complicated tools or measurements, in order to be able to take action.
How can you do that?
1. What impression of the movements results at maximum production stroke rate:
Rough, cornered, sharp transfer movements or even idle periods between the transfer motions are usually only "emergency solutions" of the setters in order to achieve a result under pressure of time and success.
The result of such effects hinder production at higher output rates, which is why the press ultimately operates at lower stroke rates.
A statement that 25 strokes / min could be achieved, but productive only 17 strokes / min is driven (deviation max to actual - stroke rate) is a clear indication of high optimization potential and should ring your alarm bells.
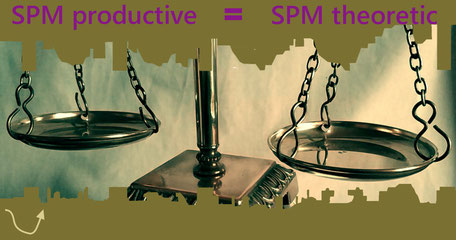
2. Check the max. strokes:
Take a look at the operating panel of your press and/or system components. Here, the achievable stroke rates of the NC 3-axis transfer and the press are visualized. In the optimal case, the maximum stroke rates that can be hit by the machine are the same for each individual axis. The output is in balance!
Exceptions confirm the rule - and must then be justified by the setter and process expert!
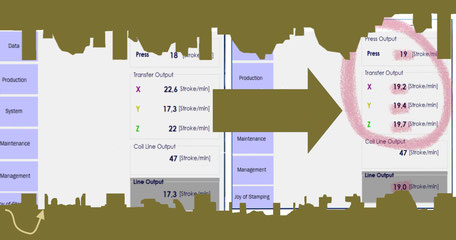
3. Observation of safety distances:
Whether in motorsport, by not keeping the ideal line and curves are driven unnecessarily far, or in athletics, if the bar is skipped far in the high jump - energy is unnecessarily used and wasted - without adding value.
Have a look to the safety distances between the moving parts of your system. At what point and how big is the smallest distance between grippers / components and the upper / lower dies at the narrowest point?
To do this best, run the system in automatic mode with the lowest number of strokes. Unnecessarily long safety distances usually mean a loss of strokes!
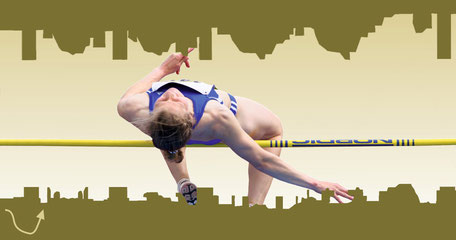
Due to sub-optimally set parameters, a lot of production capacity is lost unused. My experience shows, that the optimal setting of stamping machines quickly means 10-30% more output. All without additional investment or by modifications to tools.
This can be achieved by the ideal adjustment of the pitch and accelerations of each transfer axis. In the case of servo presses, the forming process as well as the transferring process can be extended and very detailed optimized by setting an appropriate slide curve.
Take a look at the movements on your press and check these three points. What is your impression of your production?
Would you like to experience the true potential of your sheet metal forming equipment? You would like to benchmark your output and to know how well your equipment performs? You want to get the most out of your production?
I can gladly support you in getting better:
Service: Process optimization for 3-axis transfer and progdie dies
Tasks:
- Analysis of the actual situation together with your set-up / operating personnel
- Developing a strategy for optimization based on the machine’s capabilities and features
- Improvement and optimization of press & transfer parameters
- Trial run and documentation
Facts:
Machine types:
- Servo- und conv. driven presses operated with 3-Axis transfer systems (NC) or in progdie mode
Location:
- At your machine, on site
Duration:
- Depending on die concept, app. 4-6 h/die
Don’t hesitate to get in touch with me for a request or to discuss your specific situation at any time via the contact form.