In der Produktion allgemein, aber speziell in der umformenden Fertigung dreht sich bekanntlich alles um die Ausbringungsleistung.
Das ist nicht besonders verwunderlich, da dadurch die anfallende Anlagenumlage auf mehr Bauteile aufgeteilt werden kann und somit die Fertigungskosten pro Bauteil sinken.
Die Steigerung der Taktrate einer Fertigungsanlage bewirkt demzufolge:
- Senkung Fertigungskosten pro Bauteil
- Freie Fertigungskapazitäten
► Mehr Profit!
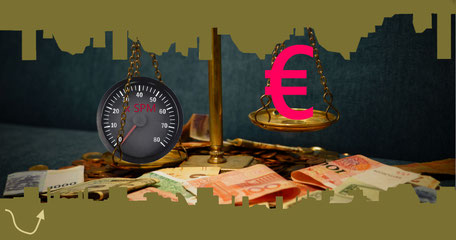
"Hubzahlsteigerung wiegt die Kosten für Prozessoptimierung auf."
Es gibt vielerlei Möglichkeiten die Ausbringungsmenge einer Fertigungsanlage zu erhöhen:
- Neu-Investition in moderne Maschinentechnologie höherer Produktivität
- Updates- & Upgrades bestehender Anlagen (Retrofit)
- Verbesserung von Betriebsmitteln (z.B. Modifikation oder Neuentwicklung von Werkzeugen)
- Verbesserung von Prozessen direkt an und im Umfeld von Anlagen (Wertstromdesign, OEE Optimierung)
Während Neuinvestitionen und Retrofits im Allgemeinen längerfristige Maßnahmen erfordern, kann durch die Verbesserung der Prozesse im Umfeld der Fertigungsanlage mit verhältnismäßig geringem Aufwand, eine beträchtliche Steigerung des Outputs erzielt werden.
Speziell an Umformautomaten kann durch die optimale Justierung der Prozessparameter von Bandvorschub, 3-Achs Transfer und Presse eine Hubzahlsteigerung erreicht werden.
Doch wie groß muss die Hubzahlsteigerung ausfallen, damit sich die Kosten für die Servicemaßnahme rechnen?
Maßgeblich für eine einfache und konservative Berechnung des wirtschaftlichen Erfolgs einer solchen Maßnahme kann der Stundensatz und die jährliche Produktionszeit der jeweiligen Fertigungsanlage herangezogen werden. Aus diesen Werten lassen sich die Betriebskosten pro Jahr berechnen. Die infolge der Optimierung erzielten Ergebnisse führen zur Steigerung der Maschinenproduktivität. Damit kann der Effekt einer Hubzahlsteigerung in einem kalkulatorischen Gewinn aufgezeigt werden. Wichtig für die Berechnung ist es aus dem Optimierungsergebnis und der Belegungszeit des jeweiligen Werkzeuges das verbesserte Produktionsvolumen der Anlage zu bestimmen.
Auf der Kostenseite sind die Kosten für die Optimierungsdienstleistung und der dadurch entstehende Produktionsausfall zu betrachten.
Diese Betrachtung ist besonders konservativ, da durch die Annahme des Stundensatzes die Kosten, nicht aber der erzielte Gewinn mit den gefertigten Bauteilen betrachtet wird. Damit eignet sich diese Art der Berechnung insbesondere zur qualitativen Bewertung der Verbesserung der Produktion.
Auf der rechten Seite sehen Sie eine beispielhafte Berechnung des Resultats einer Prozessoptimierung.
Es wurde angenommen, dass auf der Anlage insgesamt 10 Werkzeuge betrieben werden. Insgesamt wurde bei drei Werkzeugen die Taktzeit um jeweils 15%, 10% und 5% erhöht, was zu einer kalkulatorischen Steigerung des Produktionsvolumens von 4% führt. (in der Realität werden oft sehr viel höhere Werte erreicht)
Bei den exemplarisch und fiktiv angenommenen Werten für den Stundensatz ergibt dies einen kalkulatorischen Erlös der Optimierungsmaßnahme von ca. € 48.000,-.
Auf die Kosten für die Maßnahme bezogen, bedeutet dies einen Return-On-Invest von 266%.
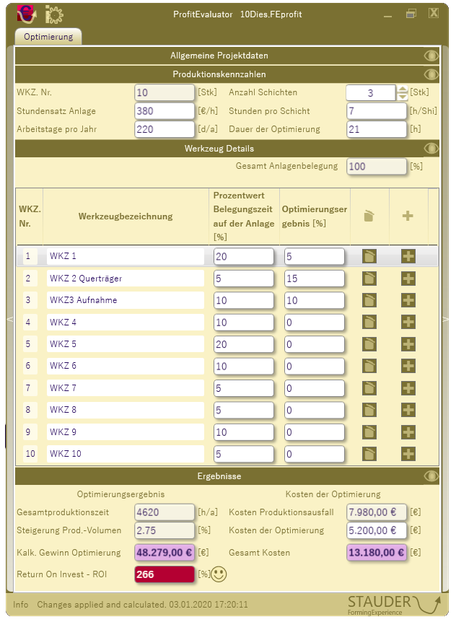
Das beeindruckt – und kann jederzeit auch ganz einfach mit Hilfe einer Tabellenkalkulation nachvollzogen werden. Obwohl dieses Ergebnis durch die vereinfachte Betrachtung über den Maschinenstundensatz konservativ ausfällt, können für die Planung der Optimierungsdienstleistung interessante Schlüsse gezogen werden.
1. Werkzeugauswahl:
Für die Optimierungsdienstleistung werden in der Regel die Werkzeuge mit den höchsten Abrufzahlen / Produktionsvolumen ausgewählt. Aus der Praxis heraus wird oft bei Werkzeugen mit geringer Fertigungsmenge eine erheblich größere Hubzahlsteigerung erzielt. Dies ist wohl darauf zurückzuführen, dass diesen Werkzeugen weniger Aufmerksamkeit geschenkt wird. Insbesondere hier lassen sich die Features von Servo-Pressen besonders gut nutzen und damit trotz geringer Belegungszeit signifikante Steigerungen des Produktionsvolumens erreichen.
2. Kosten für Produktionsausfall:
Die Optimierungsmaßnahmen an der Anlage benötigen Zeit, welche zu einem Stillstand der Produktion führt. Dies ist der Haupt-Kostentreiber in Relation zu den Gesamtkosten.
Durch eine virtuelle Durchlaufsimulation können die meisten benötigten, insbesondere freigängigkeitsrelevanten Daten virtuell und im Vorfeld der Optimierungsmaßnahme ermittelt werden. Hierdurch lässt sich der Produktionsausfall minimieren und der zusätzliche Invest in diese Dienstleistung rechtfertigen.
Nach den letzten Jahren der sehr guten Auslastung und nach einer "Oberkante-Unterlippe" Situation, in der Abrufzahlen erfüllt werden mussten, ist nun der Zeitpunkt ideal für die Steigerung der Effizienz. Nutzen Sie freigewordene Kapazitäten um Ihre Produktion wieder optimal zu trimmen.
Fühlen Sie sich als Verantwortlicher im Presswerk, der Prozess- und Ausbringungsoptimierung sowie in der Werkzeugkonstruktion angesprochen und möchten die Ausbringung Ihrer Fertigung erhöhen? …gerne freue ich mich auf Ihre Nachricht und stimme die für Ihren Fall optimale Vorgehensweise mit Ihnen ab.
Ich bedanke mich bei allen Leserinnen und Lesern meiner Artikel, für das Interesse und Feedback, und wünsche auf diesem Wege ein erfolgreiches, innovatives und optimales Jahr 2020.
Dienstleistung: Hubzahloptimierung für 3-Achs Transfer und Folgeverbundwerkzeuge
Vorgehen:
- IST-Betrachtung des Produktionsablaufs und Identifizierung von Hubzahl-Lacks (Bottlenecks) gemeinsam mit Ihrem Einrichtpersonal
- Hubzahl- und Prozessoptimierung der Einstellwerte des 3-Achs Transfer und/oder der Stößelkurve
- Ausbringungstest und weitere Optimierungsschleifen
Anlagentypen:
- Servo- und konv. angetriebene Umformautomaten im 3-Achs (NC) oder Folgeverbund Betrieb.
Ort:
- Bei Ihnen vor Ort
Dauer:
- Abhängig vom Werkzeugkonzept
ODER
Workshop: Hubzahloptimierung für 3-Achs Transfer und Folgeverbundwerkzeuge
Vorgehen:
1. Tag:
- Theorie & Grundlagen der Transfer- & Pressenprogrammierung
Folgetage:
- IST-Betrachtung des Produktionsablaufs und Identifizierung von Hubzahl-Lacks (Bottlenecks) gemeinsam mit Ihrem Einrichtpersonal
- Hubzahl- und Prozessoptimierung der Einstellwerte des 3-Achs Transfer und/oder der Stößelkurve
- Ausbringungstest und weitere Optimierungsschleifen
Zielgruppe:
Einrichter, erfahrene Bediener, Prozessoptimierer, Schichtleiter, ggf. Werkzeugkonstruktion
Anlagentypen:
- Servo- und konv. angetriebene Umformautomaten
- im 3-Achs (NC) oder Folgeverbund Betrieb.
Ort:
- Bei Ihnen vor Ort
Dauer:
- Grundmodul: 3-4 Tage
- Aufbaumodul: 3 Tage (ca. 4-6 Wochen nach Grundmodul)
Sprache & Schulungsunterlagen:
Deutsch / Englisch oder nach Vereinbarung inkl. Übersetzer