Servo presses have been in use in sheet metal forming for over a decade now and have a reputation for maximizing part output and productivity. This is proven time and time again, especially when dies are relocated from conventional presses. The reason is that this is when an objective and comparative rating of Servo's added value is clearest. The basic principle when setting up on the servo press is to maintain the slide speed in the die contact area. If, on the other hand, the dies are not in contact, the full performance of the drives is used to run through the TDC zone. Not only does this reduce the non-value-adding time and thus increase the number of strokes, but it also creates clearance for the transfer, thus enabling safe and minimal-vibration part transfer. In short, the more dynamically and flexibly the slide curve can be adapted to the situation given by the die, the higher the stroke rate will be. Since power is physically dependent on the effective drive torque and the drive rpm, it becomes clear - the more the driven slide curve deviates from the basic curve specified by the underlying press kinematics, the greater the power that must be provided by the drive system. Likewise related to increasing the stroke rate, the pendulum stroke is often used as a key feature by setters on servo presses. In this case, the situation is not as straightforward. Especially when the reduction in slide stroke is achieved by reversing the drive when the defined stroke position is reached. This is because although the potential energy decreases due to the shortened stroke, the drive torque can be greater or lower depending on the selected stroke height. A slide curve created under the pressure to produce highest amounts of stamped parts can be lowered by "smoothing" the transitions and defining corner points, which takes advantage of the press kinematics. In this way, the energy demand of the servo press is reduced.
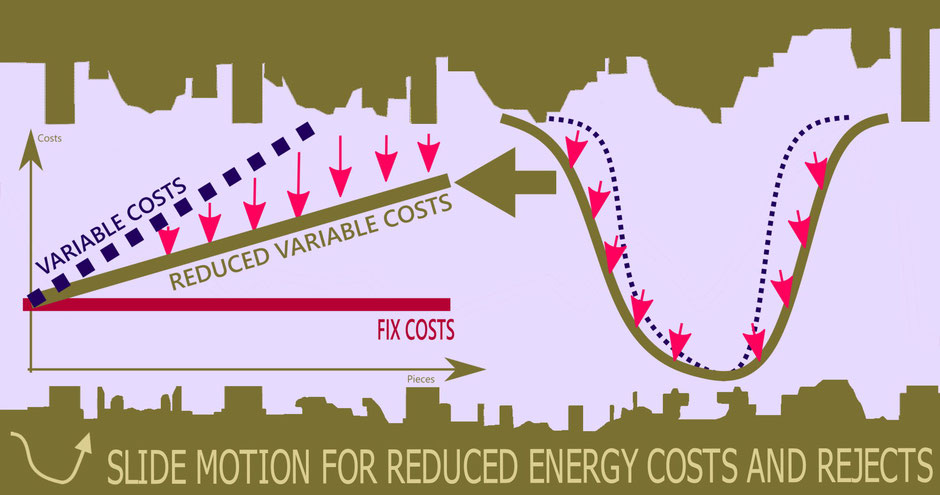
The adjusted sections of the slide curve are passed slower, but since not the entire cycle is changed, the loss of stroke rate is minor.
Summary why servo presses reach higher output rates:
On a conventional press, a process bottleneck means that the entire press cycle must be slowed down. This means that the speed is not only reduced in the actual segment of the process bottleneck, but over the entire slide movement.
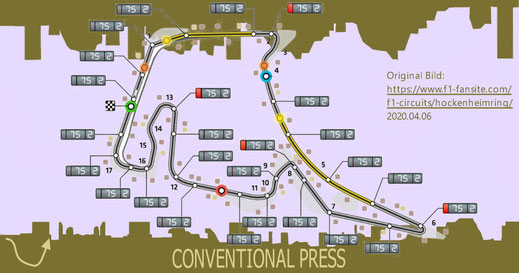
In contrast, servo technology offers the possibility of adjusting the slide speed depending on its position. It is thus possible to set the ideal speed for sheet metal part production as required.
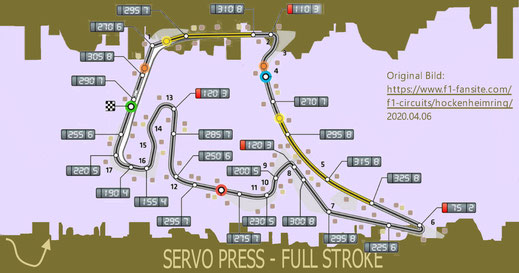
The full potential of servo technology is usually achieved by shortening the pendulum stroke. Here, the press slide is only opened just enough so that part transfer can take place unhindered. Non-productive time in the press sequence is thus minimized and the number of strokes maximized.
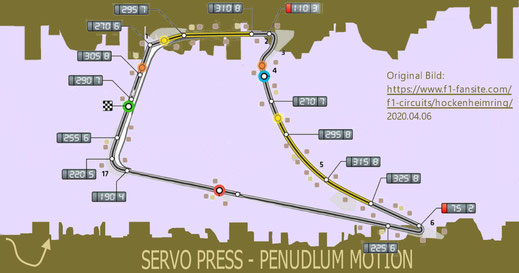
Another aspect that is usually not considered in typical stroke rate optimization is the matter of rejects. Tolerance-critical components often show a clear tendency to react sensitively to borderline high forming speeds. Thus, there is often a certain stroke rate above which the reject amount increases significantly, sometimes even one at which these problems disappear altogether. It becomes particularly interesting when rejects occur at the beginning and/or end of the respective coil or blank stack and there is a correlation to the slide speed. In such a case, it is worthwhile to reduce the forming speed by servo even more than otherwise. Although this increases the production time for a batch, it can significantly or even completely reduce the number of rejects. And here, too, the loss in stroke rate is relatively low, depending on the drawing depth and the speed to be selected, since the slide movement is only slowed down in one segment.
So, what are the reasons why the possibilities of servo technology are often not exploited in everyday business for these aspects of process optimization?
In my opinion, one of the biggest barriers in day-to-day practice is the needed time. Adapting the slide curve to the new requirements always also requires an adjustment of the setting values of the transfer and all other settings based on cam values. In order to implement optimizations in the shortest possible time, I have described the main aspects and fundamentals in a recent article „Strukturierte Einrichtprozesse an Transfer- und Servopressen" (blechnet.com, so far only available in German).
Moreover, the evaluation of the optimization results in energy per stroke or the number of rejects in comparison to the stroke rate deserves to be explained. On the one hand, if the number of strokes is achieved, the result of the optimization is available in plain text, and on the other hand, it is not necessary to first process several batches to be able to clearly attribute the reject rate to a parameter change.
Today, servo presses have a large die data storage capacity, which can typically store several hundred die data sets. This allows alternative setups for maximum stroke rate or for efficient use of resources to be held and used according to the current market situation.
Re-tune the sails and adjust them to the current market conditions. Because after all, this is why you invested at Servo and in the flexibility.
If you want to get better and make full use of your equipment, I will be happy to provide you the service of a performance benchmark to determine your performance or a stroke rate and process optimization according to your objectives.
If, on the other hand, you would like to develop the skills of your crew and get them excited about the features of servo technology, I can recommend the workshops for setters and process optimization.
I look forward to your feedback.